We offer a wide range of bearings including deep groove ball bearings, angular contact ball bearings, tapered roller bearings, cylindrical roller bearings, spherical roller bearings, thrust bearings, and many more. Our products are made from premium quality materials and manufactured using advanced technologies to ensure maximum durability and performance. We understand the importance of precision and reliability in industrial applications, hence our bearings undergo rigorous quality control checks to deliver the best results to our customers.
Our bearings are used in various industries such as automotive, agriculture, construction, mining, aerospace, energy, and many others. We have a wide network of clients across different countries, and our bearings have proven to be highly efficient in their specific applications. With our comprehensive range of products, we are confident in meeting the diverse needs of our customers and offering customized solutions for their unique requirements.
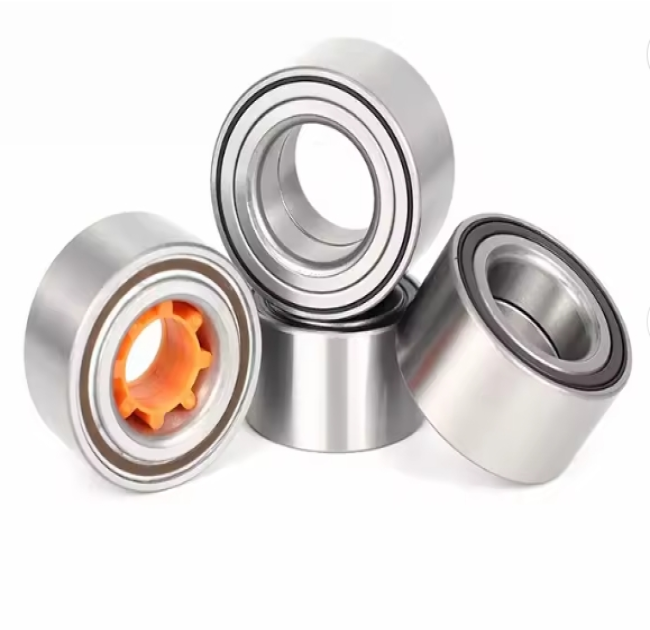
Bearing is a mechanical component that provides support and reduces friction between moving parts. It is often found in machines and equipment that require rotational movement, such as motors, wheels, and industrial machinery. The main function of a bearing is to allow smooth and efficient motion while also carrying the weight of the rotating part. Without bearings, machines and equipment would experience excessive wear and tear, leading to frequent breakdowns and costly repairs. Bearings come in different types and sizes to accommodate various load capacities and operating conditions. They are crucial in ensuring the smooth operation and longevity of many industrial and mechanical systems. With innovative designs and materials, bearings continue to play a vital role in modern technology, making our lives easier and more productive.
Bearing is an essential mechanical component that enables smooth and precise rotation of various machinery and equipment. It functions as a bridge between the moving and stationary parts, providing support and reducing friction to allow for efficient operation. With a wide range of applications in industries such as automotive, aerospace, and manufacturing, bearings play a crucial role in keeping our modern world running smoothly. They come in various types, such as ball bearings, roller bearings, and plain bearings, each designed to suit specific applications. Through continuous innovation and development, bearings have greatly improved the performance, durability, and reliability of machinery, making them an integral part of our daily lives.
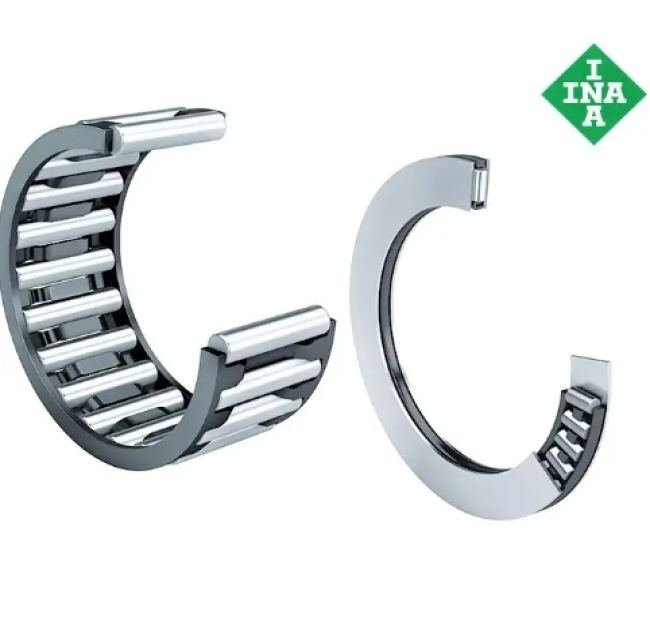
Welcome to our range of bearings. From standard ball bearings to advanced ceramic bearings, we offer a variety of high-quality products that are designed to meet the demands of various industries. Our bearings are engineered with precision and reliability in mind, ensuring smooth and efficient operation in different equipment and machinery. With our commitment to continuous innovation and excellence in manufacturing, we are dedicated to providing our customers with the best bearing solutions for their specific needs. Browse our catalog and discover the perfect bearing for your application.
2.What are the common materials used for bearing manufacturing?
3.What is the role of bearing preload in a spindle?
4.What is the difference between roller bearing and ball bearing?
5.What is the procedure for mounting a bearing?
6.How do you determine the proper amount of lubrication for a bearing?
7.How does bearing reduce friction in a rotating machine?
8.What is preloading and why is it important for high precision bearings?
9.What is the difference between thrust and radial bearings?
1.What is the difference between static and dynamic load rating for bearings?
Static load rating refers to the maximum amount of load that a bearing can withstand without permanent deformation or damage while in a stationary or non-moving state. This is typically measured in pounds or newtons. Dynamic load rating, on the other hand, refers to the maximum amount of load that a bearing can withstand while in motion or rotating at a constant speed. This rating takes into account the effects of centrifugal force and the bearing's ability to handle varying loads and speeds. It is also measured in pounds or newtons. In general, dynamic load rating is a more important factor to consider when selecting a bearing for a specific application, as most bearings are designed to operate under dynamic conditions. However, static load rating is still important for applications where the bearing may experience prolonged periods of non-movement or when the load is primarily in a vertical direction.
2.What are the common materials used for bearing manufacturing?
1. Steel: Steel is the most commonly used material for bearing manufacturing due to its high strength, durability, and resistance to wear and tear. It is also relatively inexpensive and readily available. 2. Ceramic: Ceramic bearings are becoming increasingly popular due to their high strength, low friction, and resistance to corrosion and wear. They are commonly used in high-speed and high-temperature applications. 3. Bronze: Bronze bearings are commonly used in applications where high load capacity and low speed are required. They are also resistant to corrosion and have good thermal conductivity. 4. Plastic: Plastic bearings are lightweight, corrosion-resistant, and have good self-lubricating properties. They are commonly used in applications where low friction and low noise are important. 5. Brass: Brass bearings are commonly used in low-speed and low-load applications. They have good corrosion resistance and are relatively inexpensive. 6. Aluminum: Aluminum bearings are lightweight, corrosion-resistant, and have good thermal conductivity. They are commonly used in applications where weight is a critical factor. 7. Tungsten Carbide: Tungsten carbide bearings are extremely hard and wear-resistant, making them suitable for high-load and high-speed applications. They are commonly used in industrial machinery and equipment. 8. Titanium: Titanium bearings are lightweight, corrosion-resistant, and have good strength and stiffness. They are commonly used in aerospace and medical applications. 9. Graphite: Graphite bearings have excellent self-lubricating properties and can operate at high temperatures. They are commonly used in high-temperature and high-speed applications. 10. Glass: Glass bearings are used in applications where chemical resistance and high precision are required. They are commonly used in laboratory equipment and scientific instruments.
3.What is the role of bearing preload in a spindle?
Bearing preload is the intentional application of a slight load or tension on the bearings in a spindle. This preload helps to eliminate any internal clearance or play in the bearings, ensuring that they are in constant contact with each other and with the spindle shaft. The role of bearing preload in a spindle is to improve the overall stiffness and accuracy of the spindle, as well as to reduce vibration and noise during operation. It also helps to distribute the load evenly across the bearings, increasing their lifespan and reducing the risk of premature failure. Additionally, bearing preload can improve the responsiveness and precision of the spindle, making it more suitable for high-speed and high-precision machining applications.
4.What is the difference between roller bearing and ball bearing?
Roller bearings and ball bearings are both types of anti-friction bearings that are used to reduce friction between moving parts. They both work by using rolling elements to separate the moving parts and allow them to move smoothly and efficiently. However, there are some key differences between the two types of bearings. 1. Shape and Design: The main difference between roller bearings and ball bearings is their shape and design. Roller bearings have cylindrical rolling elements, while ball bearings have spherical rolling elements. This difference in shape affects the way the bearings distribute the load and handle different types of forces. 2. Load Capacity: Due to their cylindrical shape, roller bearings have a larger contact area with the raceway, which allows them to handle heavier loads than ball bearings. This makes roller bearings more suitable for applications with high radial or axial loads. 3. Friction and Speed: Ball bearings have a smaller contact area with the raceway, which results in lower friction and allows them to operate at higher speeds than roller bearings. This makes ball bearings more suitable for applications that require high speeds and low friction. 4. Cost: In general, roller bearings are more expensive than ball bearings due to their larger size and higher load capacity. This makes ball bearings a more cost-effective option for applications that do not require heavy loads. 5. Noise and Vibration: Roller bearings tend to produce more noise and vibration compared to ball bearings due to their larger contact area and higher load capacity. This makes ball bearings a better choice for applications that require smooth and quiet operation. 6. Applications: Both roller bearings and ball bearings have their own unique advantages and are used in a wide range of applications. Roller bearings are commonly used in heavy-duty applications such as automotive and industrial machinery, while ball bearings are more commonly used in lighter applications such as household appliances and electric motors. In summary, the main differences between roller bearings and ball bearings are their shape, load capacity, friction and speed, cost, noise and vibration, and applications. The choice between the two types of bearings depends on the specific requirements of the application and the type of load it needs to handle.
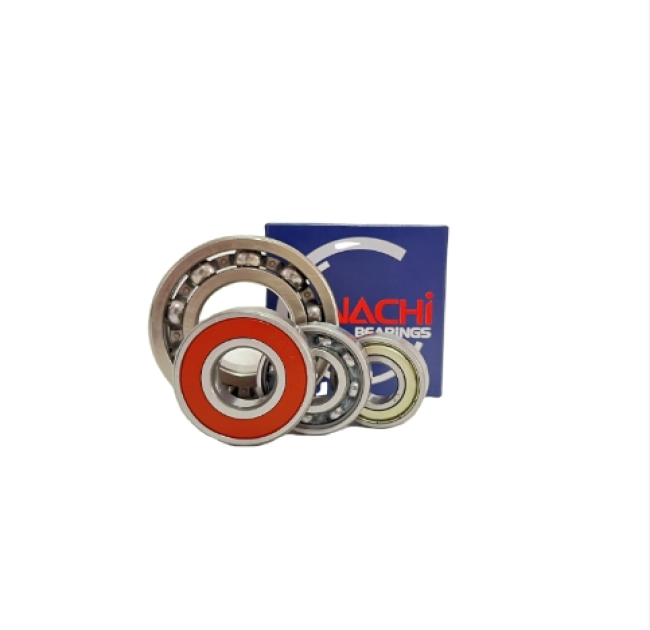
5.What is the procedure for mounting a bearing?
1. Gather Materials: Before starting the procedure, make sure you have all the necessary materials such as the bearing, mounting tools, lubricant, and cleaning supplies. 2. Clean the Shaft and Housing: Use a degreaser or solvent to clean the shaft and housing where the bearing will be mounted. This will ensure a clean and smooth surface for the bearing to be mounted on. 3. Inspect the Bearing: Before mounting the bearing, inspect it for any damage or defects. If there are any issues, do not proceed with the mounting process and replace the bearing. 4. Apply Lubricant: Apply a thin layer of lubricant to the shaft and housing to reduce friction and aid in the mounting process. 5. Position the Bearing: Place the bearing on the shaft or in the housing, depending on the type of bearing. Make sure it is properly aligned and seated in the correct position. 6. Use Mounting Tools: Use a mounting tool, such as a press or hammer, to apply even pressure to the bearing and press it onto the shaft or into the housing. Be careful not to damage the bearing during this process. 7. Check for Proper Fit: Once the bearing is mounted, check for proper fit by rotating the shaft or housing. The bearing should rotate smoothly without any binding or excessive play. 8. Secure the Bearing: If necessary, secure the bearing in place with a retaining ring or locking mechanism. 9. Clean and Lubricate: Wipe away any excess lubricant and clean the surrounding area. Apply a final layer of lubricant to the bearing to ensure smooth operation. 10. Test the Bearing: After mounting, test the bearing to ensure it is functioning properly. If there are any issues, recheck the mounting process or replace the bearing. 11. Repeat for Multiple Bearings: If you are mounting multiple bearings, repeat the process for each one, making sure to clean and lubricate the shaft and housing before mounting each bearing. 12. Dispose of Materials: Properly dispose of any used materials and clean up the work area.
6.How do you determine the proper amount of lubrication for a bearing?
The proper amount of lubrication for a bearing can be determined by following these steps: 1. Check the manufacturer's recommendations: The first step is to check the manufacturer's recommendations for the specific bearing. They will usually provide guidelines for the type and amount of lubricant to use. 2. Consider the operating conditions: The amount of lubrication needed will depend on the operating conditions of the bearing. Factors such as speed, load, temperature, and environment should be taken into account. 3. Calculate the lubrication interval: The lubrication interval is the time or distance between lubrication cycles. It can be calculated by dividing the bearing's rated life by the operating hours or distance. 4. Determine the lubrication quantity: The lubrication quantity is the amount of lubricant needed for each lubrication cycle. It can be calculated by multiplying the bearing's capacity factor by the bearing's internal volume. 5. Use a lubrication chart: Many manufacturers provide lubrication charts that specify the recommended lubrication quantity based on the bearing size and operating conditions. 6. Monitor the bearing: It is important to monitor the bearing regularly to ensure that it is receiving the proper amount of lubrication. If the bearing shows signs of inadequate lubrication, such as increased noise or heat, the lubrication interval or quantity may need to be adjusted. 7. Consult a lubrication expert: If you are unsure about the proper amount of lubrication for a bearing, it is best to consult a lubrication expert who can provide specific recommendations based on your application.
7.How does bearing reduce friction in a rotating machine?
Bearing is a mechanical component that supports the rotating shaft of a machine and allows it to rotate with minimal friction. It reduces friction in a rotating machine in the following ways: 1. Separation of Surfaces: Bearings create a small gap between the rotating shaft and the stationary part of the machine, such as the housing or frame. This separation of surfaces reduces the contact area between them, thereby reducing friction. 2. Rolling or Sliding Motion: Bearings are designed to facilitate either rolling or sliding motion between the rotating shaft and the stationary part. This motion reduces the frictional force between the two surfaces, making it easier for the shaft to rotate. 3. Lubrication: Bearings are often lubricated with oil or grease to further reduce friction. The lubricant forms a thin film between the surfaces, reducing direct contact and minimizing friction. 4. Smooth Surface: Bearings are made with precision and have a smooth surface, which helps in reducing friction. The smooth surface allows the rotating shaft to move with minimal resistance, resulting in lower friction. 5. Load Distribution: Bearings distribute the load of the rotating shaft evenly over a larger area, reducing the pressure on any one point. This helps in reducing friction and wear on the surfaces in contact. 6. Absorption of Shock and Vibration: Bearings also help in absorbing shock and vibration, which can cause friction and wear in a rotating machine. This is especially important in high-speed machines where even small amounts of friction can cause significant damage. In summary, bearings reduce friction in a rotating machine by creating a small gap between surfaces, facilitating rolling or sliding motion, lubricating the surfaces, providing a smooth surface, distributing the load, and absorbing shock and vibration.
8.What is preloading and why is it important for high precision bearings?
Preloading is the application of a controlled axial load on a bearing before it is put into service. This load is designed to eliminate any internal clearance within the bearing, ensuring that the rolling elements are in constant contact with the raceways. This is important for high precision bearings because it helps to reduce or eliminate any potential play or movement within the bearing, which can affect its accuracy and performance. Preloading is important for high precision bearings because it helps to improve their stiffness and rigidity, which is crucial for applications that require precise positioning and motion control. It also helps to distribute the load evenly across the bearing, reducing the risk of localized stress and wear. Additionally, preloading can help to improve the bearing's ability to withstand high speeds and heavy loads, making it more reliable and durable in demanding operating conditions. Overall, preloading is an essential step in the manufacturing and installation process of high precision bearings, ensuring that they are able to meet the strict requirements of precision applications.
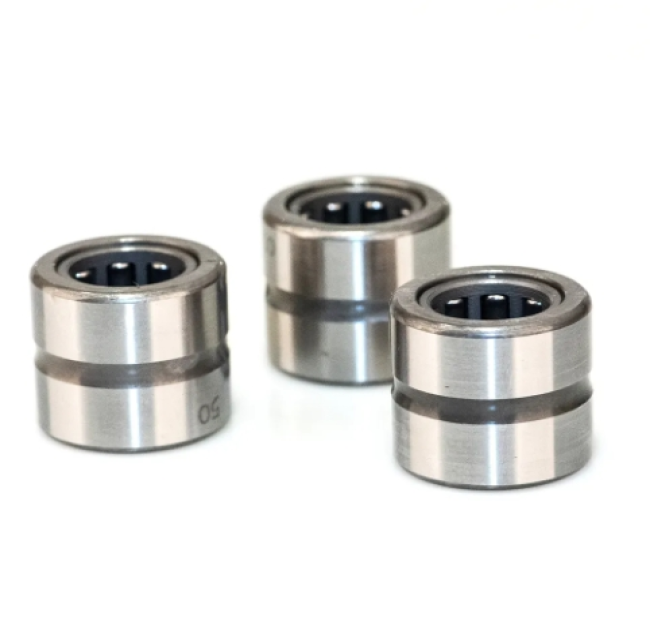
9.What is the difference between thrust and radial bearings?
Thrust bearings are designed to handle axial loads, or forces that act parallel to the axis of rotation. They are typically used in applications where there is a need to support a heavy load in one direction, such as in a car engine or a wind turbine. Radial bearings, on the other hand, are designed to handle radial loads, or forces that act perpendicular to the axis of rotation. They are commonly used in applications where there is a need to support a rotating shaft, such as in a bicycle wheel or a conveyor belt. In summary, the main difference between thrust and radial bearings is the direction of the load they are designed to support. Thrust bearings handle axial loads, while radial bearings handle radial loads.