Our company is committed to providing our customers with the best solutions for their bearing needs, including a wide range of products from world-renowned manufacturers such as SKF, NSK, and NTN. We also have our own brand of bearings that are manufactured with the highest standards to ensure durability and reliability.
Our product line includes deep groove ball bearings, spherical roller bearings, cylindrical roller bearings, and many others. We offer various sizes and configurations to accommodate different applications and operating conditions. Our bearings are widely used in a variety of industries, including automotive, aerospace, agriculture, and mining.
At Bearing, we understand the importance of quality and customer satisfaction. That is why we have a team of experienced professionals who are dedicated to providing excellent service and technical support to our customers. We also have state-of-the-art facilities and advanced equipment to ensure the accuracy and precision of our products.
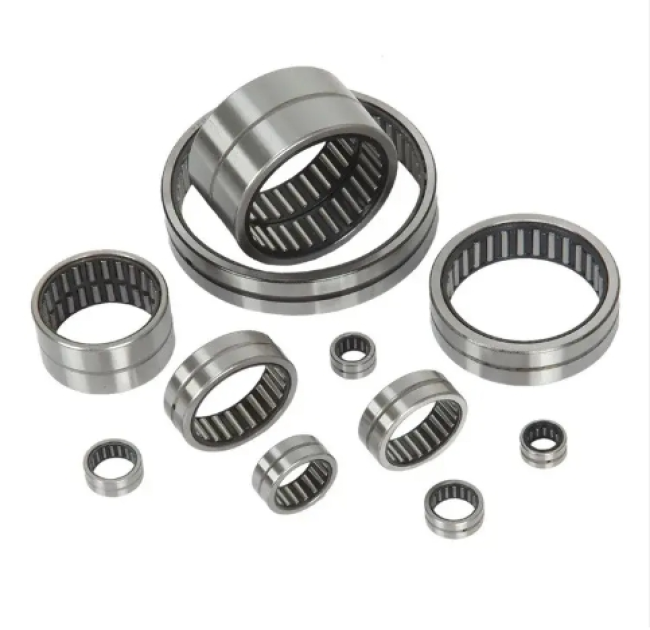
Bearing is an essential mechanical component that enables smooth and precise rotation of various machinery and equipment. It functions as a bridge between the moving and stationary parts, providing support and reducing friction to allow for efficient operation. With a wide range of applications in industries such as automotive, aerospace, and manufacturing, bearings play a crucial role in keeping our modern world running smoothly. They come in various types, such as ball bearings, roller bearings, and plain bearings, each designed to suit specific applications. Through continuous innovation and development, bearings have greatly improved the performance, durability, and reliability of machinery, making them an integral part of our daily lives.
A bearing is a mechanical component used to reduce friction between moving parts. It consists of a cylindrical or conical shape, usually made out of metal, with balls or rollers inside. The balls or rollers are held in place by a race, which is a ring-shaped groove that keeps them evenly spaced and allows them to rotate freely. Bearings are commonly used in machinery, automotive parts, and other industrial applications to support and guide moving parts, such as wheels, shafts, and axles, and to enable smooth and efficient operation. With the advancement of technology, bearings have also become more sophisticated and can now vary in size, shape, material, and design to suit different purposes. Overall, bearings play a critical role in reducing friction and ensuring precise movement, making them an essential component in various mechanical systems.
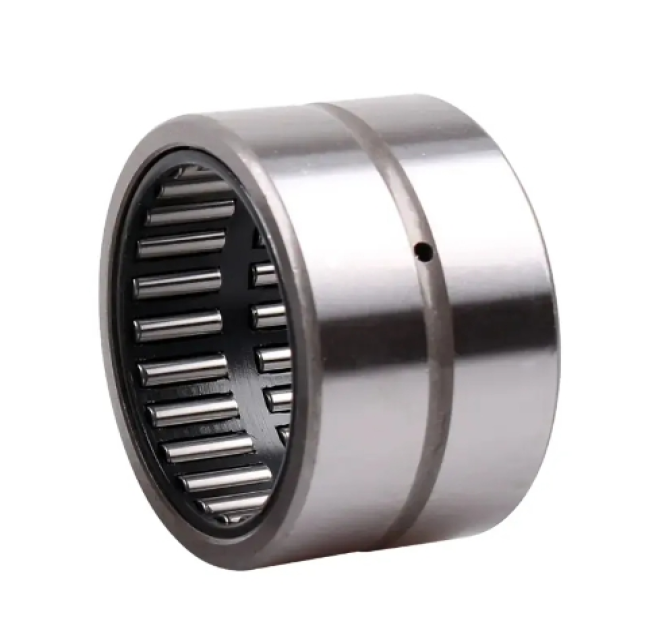
Welcome to our range of bearings. From standard ball bearings to advanced ceramic bearings, we offer a variety of high-quality products that are designed to meet the demands of various industries. Our bearings are engineered with precision and reliability in mind, ensuring smooth and efficient operation in different equipment and machinery. With our commitment to continuous innovation and excellence in manufacturing, we are dedicated to providing our customers with the best bearing solutions for their specific needs. Browse our catalog and discover the perfect bearing for your application.
2.How does bearing handle axial load and what type of bearing is suitable for this?
3.What is the effect of misalignment on bearing performance?
4.How does improper bearing installation impact its performance?
5.What is the difference between roller bearing and ball bearing?
6.Can bearings be reused or should they always be replaced?
7.What is the difference between thrust and radial bearings?
8.What is the difference between static and dynamic load rating for bearings?
9.What is bearing preload and when is it necessary?
1.How does temperature affect bearing performance?
Temperature can have a significant impact on bearing performance in several ways: 1. Lubrication: High temperatures can cause lubricants to break down or evaporate, leading to inadequate lubrication and increased friction between bearing components. This can result in premature wear and failure of the bearing. 2. Material expansion: As temperature increases, the materials used in bearings can expand, causing changes in the internal clearance and fit of the bearing. This can lead to increased friction and reduced bearing life. 3. Thermal expansion mismatch: Bearings are often made of different materials with different coefficients of thermal expansion. When exposed to high temperatures, these materials can expand at different rates, causing stress and potential damage to the bearing. 4. Thermal shock: Rapid changes in temperature can cause thermal shock, which can lead to cracking or distortion of bearing components. 5. Corrosion: High temperatures can accelerate the corrosion process, leading to pitting and other forms of damage to bearing surfaces. 6. Viscosity changes: The viscosity of lubricants can change with temperature, affecting their ability to form a protective film between bearing surfaces. This can result in increased friction and wear. To ensure optimal bearing performance, it is important to consider the operating temperature and choose bearings and lubricants that can withstand the expected temperature range. Regular maintenance and monitoring of bearing temperature can also help identify potential issues and prevent premature failure.
2.How does bearing handle axial load and what type of bearing is suitable for this?
Bearing handles axial load by using rolling elements such as balls or rollers to distribute the load evenly along the axis of rotation. This allows the bearing to support the weight or force applied in a linear direction, without causing excessive friction or wear. The type of bearing suitable for handling axial load depends on the specific application and the magnitude of the load. Some common types of bearings that are suitable for handling axial load include: 1. Thrust ball bearings: These bearings consist of two grooved washers and a cage with balls in between. They are designed to handle axial loads in one direction and are commonly used in applications such as automotive transmissions and machine tool spindles. 2. Tapered roller bearings: These bearings have tapered rollers arranged in a single row, allowing them to handle both radial and axial loads. They are commonly used in heavy-duty applications such as truck axles and gearboxes. 3. Cylindrical roller bearings: These bearings have cylindrical rollers arranged in a single row and are suitable for handling high radial and axial loads. They are commonly used in applications such as machine tool spindles and heavy-duty gearboxes. 4. Spherical roller bearings: These bearings have barrel-shaped rollers and are designed to handle high radial and axial loads. They are commonly used in applications such as heavy-duty conveyor systems and large industrial gearboxes. It is important to select the right type of bearing for the specific application to ensure optimal performance and longevity. Factors such as load capacity, speed, and operating conditions should be considered when choosing a bearing for handling axial load.

3.What is the effect of misalignment on bearing performance?
Misalignment occurs when the centerlines of the bearing and the shaft are not aligned properly. This can have several negative effects on bearing performance, including: 1. Increased friction and wear: Misalignment causes the bearing to operate at an angle, which increases the contact area between the bearing and the shaft. This results in increased friction and wear, leading to premature bearing failure. 2. Reduced load capacity: Misalignment can reduce the load capacity of the bearing, as it is not able to distribute the load evenly across its surface. This can result in overloading and premature failure of the bearing. 3. Vibration and noise: Misalignment can cause the bearing to vibrate and produce noise, which can affect the overall performance of the machinery. This can also lead to increased stress on other components, resulting in further damage. 4. Reduced efficiency: Misalignment can also reduce the efficiency of the bearing, as it is not able to rotate smoothly. This can result in increased energy consumption and decreased performance of the machinery. 5. Lubrication issues: Misalignment can also affect the distribution of lubricant within the bearing, leading to inadequate lubrication and increased friction. This can result in overheating and premature failure of the bearing. Overall, misalignment can significantly reduce the lifespan and performance of bearings, leading to increased maintenance costs and downtime for machinery. It is important to ensure proper alignment during installation and regular maintenance to avoid these negative effects.
4.How does improper bearing installation impact its performance?
Improper bearing installation can have a significant impact on its performance in several ways: 1. Reduced load capacity: If the bearing is not installed correctly, it may not be able to handle the intended load, leading to premature failure and reduced performance. 2. Increased friction and heat generation: Incorrect installation can result in misalignment or uneven distribution of load, causing increased friction and heat generation. This can lead to accelerated wear and tear of the bearing and reduced performance. 3. Vibration and noise: Improper installation can cause the bearing to operate at an angle, resulting in vibration and noise. This can affect the overall performance of the machinery and lead to premature failure. 4. Reduced lifespan: A bearing that is not installed correctly may not be able to withstand the expected operating conditions, leading to premature failure and reduced lifespan. 5. Safety hazards: In some cases, improper bearing installation can result in catastrophic failure, posing a safety hazard to the operators and surrounding equipment. 6. Costly repairs and downtime: If a bearing fails due to improper installation, it can result in costly repairs and downtime, affecting the overall productivity and profitability of the machinery. Overall, improper bearing installation can significantly impact its performance, leading to reduced efficiency, increased maintenance costs, and safety risks. It is essential to follow proper installation procedures and guidelines to ensure optimal performance and longevity of the bearing.
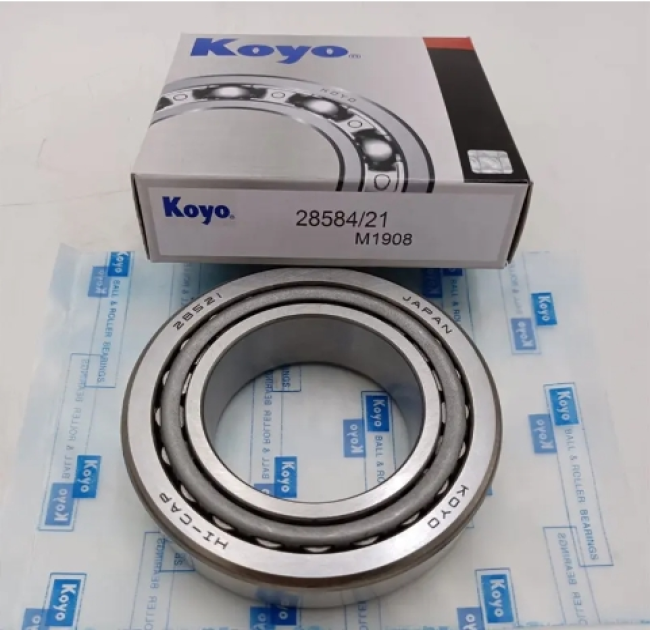
5.What is the difference between roller bearing and ball bearing?
Roller bearings and ball bearings are both types of anti-friction bearings that are used to reduce friction between moving parts. They both work by using rolling elements to separate the moving parts and allow them to move smoothly and efficiently. However, there are some key differences between the two types of bearings. 1. Shape and Design: The main difference between roller bearings and ball bearings is their shape and design. Roller bearings have cylindrical rolling elements, while ball bearings have spherical rolling elements. This difference in shape affects the way the bearings distribute the load and handle different types of forces. 2. Load Capacity: Due to their cylindrical shape, roller bearings have a larger contact area with the raceway, which allows them to handle heavier loads than ball bearings. This makes roller bearings more suitable for applications with high radial or axial loads. 3. Friction and Speed: Ball bearings have a smaller contact area with the raceway, which results in lower friction and allows them to operate at higher speeds than roller bearings. This makes ball bearings more suitable for applications that require high speeds and low friction. 4. Cost: In general, roller bearings are more expensive than ball bearings due to their larger size and higher load capacity. This makes ball bearings a more cost-effective option for applications that do not require heavy loads. 5. Noise and Vibration: Roller bearings tend to produce more noise and vibration compared to ball bearings due to their larger contact area and higher load capacity. This makes ball bearings a better choice for applications that require smooth and quiet operation. 6. Applications: Both roller bearings and ball bearings have their own unique advantages and are used in a wide range of applications. Roller bearings are commonly used in heavy-duty applications such as automotive and industrial machinery, while ball bearings are more commonly used in lighter applications such as household appliances and electric motors. In summary, the main differences between roller bearings and ball bearings are their shape, load capacity, friction and speed, cost, noise and vibration, and applications. The choice between the two types of bearings depends on the specific requirements of the application and the type of load it needs to handle.
6.Can bearings be reused or should they always be replaced?
It depends on the type and condition of the bearing. In general, it is recommended to replace bearings rather than reusing them, as they can wear out over time and may not perform as well as a new bearing. However, if the bearing is in good condition and has not been subjected to excessive wear or damage, it may be possible to reuse it. It is always best to consult with a professional mechanic or manufacturer for specific recommendations on whether a bearing can be reused or should be replaced.
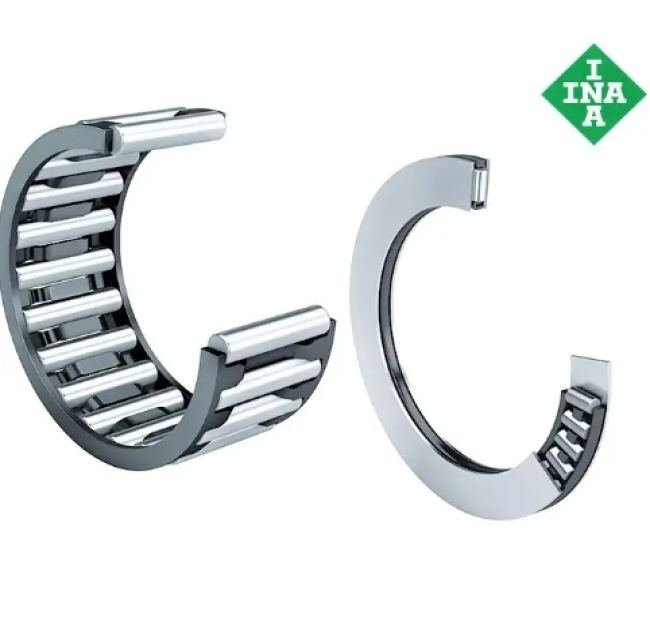
7.What is the difference between thrust and radial bearings?
Thrust bearings are designed to handle axial loads, or forces that act parallel to the axis of rotation. They are typically used in applications where there is a need to support a heavy load in one direction, such as in a car engine or a wind turbine. Radial bearings, on the other hand, are designed to handle radial loads, or forces that act perpendicular to the axis of rotation. They are commonly used in applications where there is a need to support a rotating shaft, such as in a bicycle wheel or a conveyor belt. In summary, the main difference between thrust and radial bearings is the direction of the load they are designed to support. Thrust bearings handle axial loads, while radial bearings handle radial loads.
8.What is the difference between static and dynamic load rating for bearings?
Static load rating refers to the maximum amount of load that a bearing can withstand without permanent deformation or damage while in a stationary or non-moving state. This is typically measured in pounds or newtons. Dynamic load rating, on the other hand, refers to the maximum amount of load that a bearing can withstand while in motion or rotating at a constant speed. This rating takes into account the effects of centrifugal force and the bearing's ability to handle varying loads and speeds. It is also measured in pounds or newtons. In general, dynamic load rating is a more important factor to consider when selecting a bearing for a specific application, as most bearings are designed to operate under dynamic conditions. However, static load rating is still important for applications where the bearing may experience prolonged periods of non-movement or when the load is primarily in a vertical direction.
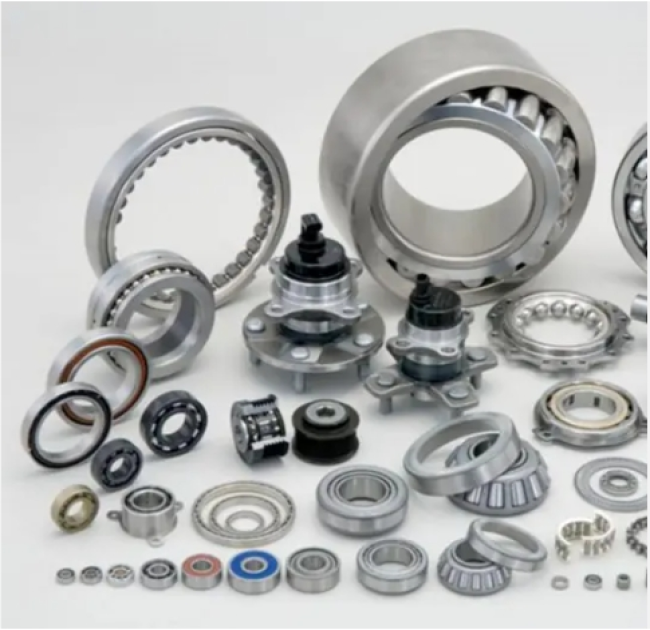
9.What is bearing preload and when is it necessary?
Bearing preload is the application of a slight amount of force or tension on the bearings in a machine or mechanism. This force helps to eliminate any internal clearance or play in the bearings, ensuring that they are in constant contact with the rotating parts. Bearing preload is necessary in applications where there is a need for high precision and accuracy, such as in high-speed machines or precision instruments. It is also used in applications where there is a risk of vibration or shock, as preload helps to prevent the bearings from moving or shifting during these events. In addition, bearing preload can help to improve the overall performance and lifespan of the bearings by reducing wear and increasing stiffness. It is commonly used in automotive and aerospace industries, as well as in high-precision machinery and equipment.