we offer a wide range of bearings to meet the diverse needs of our customers. Our product line includes ball bearings, roller bearings, tapered roller bearings, spherical bearings, and many more. We work with top manufacturers to ensure that our products are of the highest quality and meet international standards. We also have a team of experienced engineers who can assist our customers in selecting the right bearing for their specific applications.
Another popular product in our inventory is the tapered roller bearing. This type of bearing is commonly used in automotive and agricultural equipment and is known for its ability to handle both radial and axial loads. We offer tapered roller bearings in various sizes and designs to meet the specific requirements of our customers.
At Bearing Dealer, we understand the importance of quality and reliability when it comes to bearings. Therefore, we only source our products from trusted manufacturers and conduct rigorous quality control to ensure that our customers receive the best products. We also offer competitive prices and timely delivery to make sure our customers' needs are met.
In addition to our wide range of bearings, we also provide exceptional customer service. Our team is highly knowledgeable and can provide technical support and assistance to our clients. We value our customers and strive to build long-lasting relationships with them.
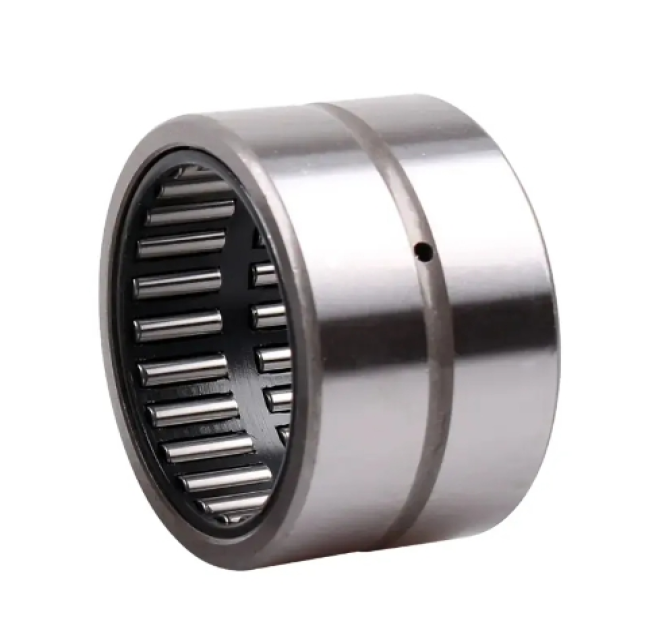
A bearing is a mechanical component used to reduce friction between moving parts. It consists of a cylindrical or conical shape, usually made out of metal, with balls or rollers inside. The balls or rollers are held in place by a race, which is a ring-shaped groove that keeps them evenly spaced and allows them to rotate freely. Bearings are commonly used in machinery, automotive parts, and other industrial applications to support and guide moving parts, such as wheels, shafts, and axles, and to enable smooth and efficient operation. With the advancement of technology, bearings have also become more sophisticated and can now vary in size, shape, material, and design to suit different purposes. Overall, bearings play a critical role in reducing friction and ensuring precise movement, making them an essential component in various mechanical systems.
Bearing is a mechanical component that provides support and reduces friction between moving parts. It is often found in machines and equipment that require rotational movement, such as motors, wheels, and industrial machinery. The main function of a bearing is to allow smooth and efficient motion while also carrying the weight of the rotating part. Without bearings, machines and equipment would experience excessive wear and tear, leading to frequent breakdowns and costly repairs. Bearings come in different types and sizes to accommodate various load capacities and operating conditions. They are crucial in ensuring the smooth operation and longevity of many industrial and mechanical systems. With innovative designs and materials, bearings continue to play a vital role in modern technology, making our lives easier and more productive.

Welcome to our range of bearings. From standard ball bearings to advanced ceramic bearings, we offer a variety of high-quality products that are designed to meet the demands of various industries. Our bearings are engineered with precision and reliability in mind, ensuring smooth and efficient operation in different equipment and machinery. With our commitment to continuous innovation and excellence in manufacturing, we are dedicated to providing our customers with the best bearing solutions for their specific needs. Browse our catalog and discover the perfect bearing for your application.
2.How do you disassemble a bearing for maintenance or replacement?
3.What is the procedure for mounting a bearing?
4.What are the different types of bearing and their applications?
5.What is the benefit of using ceramic bearings?
6.How do you calculate the expected lifespan of a bearing?
7.What is the difference between bearing life and bearing reliability?
8.How can you extend the lifespan of a bearing?
9.How does improper bearing installation impact its performance?
1.How do you determine the expected speed limit for a bearing?
The expected speed limit for a bearing can be determined by considering several factors, including the type of bearing, the load and operating conditions, and the lubrication used. 1. Bearing type: Different types of bearings have different speed limits. For example, roller bearings can typically handle higher speeds than ball bearings. 2. Load and operating conditions: The expected speed limit for a bearing will also depend on the load and operating conditions it will be subjected to. Higher loads and harsh operating conditions can decrease the speed limit of a bearing. 3. Lubrication: Proper lubrication is crucial for the smooth operation of bearings at high speeds. The type and quality of lubricant used can affect the expected speed limit of a bearing. 4. Manufacturer's specifications: The manufacturer of the bearing will provide information on the maximum recommended speed limit for the bearing. This information should be followed to ensure safe and efficient operation. 5. Bearing materials and design: The materials and design of the bearing can also impact its speed limit. Bearings made with high-quality materials and advanced designs can typically handle higher speeds. It is important to note that the expected speed limit is not a fixed value and can vary depending on the specific application and conditions. Regular maintenance and proper handling can also help extend the speed limit of a bearing.
2.How do you disassemble a bearing for maintenance or replacement?
1. Gather necessary tools and materials: You will need a hammer, a punch or small screwdriver, a bearing puller (if available), a clean cloth, and replacement bearings. 2. Remove any retaining rings or snap rings: Some bearings may have retaining rings or snap rings that hold them in place. Use a pair of pliers to remove these before attempting to disassemble the bearing. 3. Place the bearing on a solid surface: Place the bearing on a solid surface with the outer race facing down. This will allow you to access the inner race and rollers. 4. Remove the seal or shield: If the bearing has a seal or shield, use a small screwdriver or punch to gently pry it off. Be careful not to damage the seal or shield as it may need to be reused. 5. Remove the inner race: Use a punch or small screwdriver to tap the inner race out of the bearing. Be sure to tap evenly around the race to avoid damaging it. 6. Remove the rollers or balls: Once the inner race is removed, the rollers or balls should easily come out. If they are stuck, use a punch or small screwdriver to gently pry them out. 7. Clean the bearing components: Use a clean cloth to wipe down all the bearing components, including the inner and outer races, rollers or balls, and any seals or shields. 8. Inspect for damage: Take a close look at all the components to check for any signs of damage or wear. If any parts are damaged, they will need to be replaced. 9. Replace any damaged components: If any parts are damaged, replace them with new ones. It is important to use the correct size and type of bearing for your specific application. 10. Reassemble the bearing: Once all the components are clean and in good condition, reassemble the bearing in the reverse order of disassembly. Make sure all parts are properly aligned and seated. 11. Install the bearing back into the machine: Once the bearing is reassembled, it can be installed back into the machine. Use a bearing puller if necessary to press the bearing back into place. 12. Lubricate the bearing: Before using the machine, be sure to lubricate the bearing with the appropriate lubricant to ensure smooth operation. 13. Dispose of old bearings properly: If the old bearings are damaged or worn beyond repair, be sure to dispose of them properly according to local regulations.
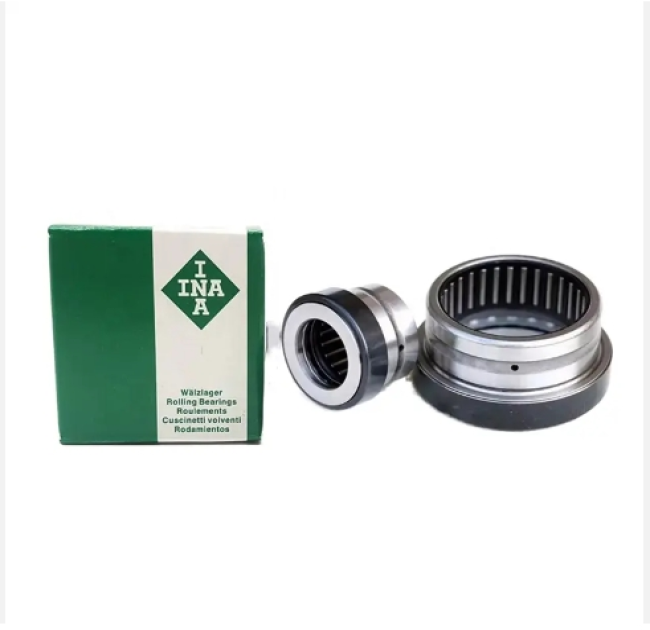
3.What is the procedure for mounting a bearing?
1. Gather Materials: Before starting the procedure, make sure you have all the necessary materials such as the bearing, mounting tools, lubricant, and cleaning supplies. 2. Clean the Shaft and Housing: Use a degreaser or solvent to clean the shaft and housing where the bearing will be mounted. This will ensure a clean and smooth surface for the bearing to be mounted on. 3. Inspect the Bearing: Before mounting the bearing, inspect it for any damage or defects. If there are any issues, do not proceed with the mounting process and replace the bearing. 4. Apply Lubricant: Apply a thin layer of lubricant to the shaft and housing to reduce friction and aid in the mounting process. 5. Position the Bearing: Place the bearing on the shaft or in the housing, depending on the type of bearing. Make sure it is properly aligned and seated in the correct position. 6. Use Mounting Tools: Use a mounting tool, such as a press or hammer, to apply even pressure to the bearing and press it onto the shaft or into the housing. Be careful not to damage the bearing during this process. 7. Check for Proper Fit: Once the bearing is mounted, check for proper fit by rotating the shaft or housing. The bearing should rotate smoothly without any binding or excessive play. 8. Secure the Bearing: If necessary, secure the bearing in place with a retaining ring or locking mechanism. 9. Clean and Lubricate: Wipe away any excess lubricant and clean the surrounding area. Apply a final layer of lubricant to the bearing to ensure smooth operation. 10. Test the Bearing: After mounting, test the bearing to ensure it is functioning properly. If there are any issues, recheck the mounting process or replace the bearing. 11. Repeat for Multiple Bearings: If you are mounting multiple bearings, repeat the process for each one, making sure to clean and lubricate the shaft and housing before mounting each bearing. 12. Dispose of Materials: Properly dispose of any used materials and clean up the work area.
4.What are the different types of bearing and their applications?
1. Ball bearings: These are the most common type of bearings and are used in a wide range of applications, including automotive, industrial, and household appliances. They consist of a series of balls held in place by a cage, which allows for smooth rotation and reduces friction. 2. Roller bearings: These bearings use cylindrical or tapered rollers instead of balls to distribute the load evenly. They are commonly used in heavy-duty applications such as conveyor systems, gearboxes, and large industrial machinery. 3. Thrust bearings: These bearings are designed to handle axial loads, which are forces that act parallel to the bearing's axis. They are commonly used in automotive and aerospace applications, as well as in heavy machinery. 4. Spherical bearings: These bearings have a spherical inner and outer race, allowing them to accommodate misalignment and angular movement. They are commonly used in applications where there is a need for flexibility, such as in suspension systems and steering columns. 5. Needle bearings: These bearings use long, thin rollers instead of balls to reduce friction and handle high radial loads. They are commonly used in applications with limited space, such as in small motors and appliances. 6. Tapered roller bearings: These bearings have tapered rollers and are designed to handle both radial and axial loads. They are commonly used in automotive and industrial applications, such as wheel bearings and gearboxes. 7. Magnetic bearings: These bearings use magnetic fields to support and guide the rotating shaft, eliminating the need for physical contact between the bearing and the shaft. They are commonly used in high-speed and high-precision applications, such as in turbines and compressors. 8. Fluid bearings: These bearings use a thin layer of fluid, such as oil or air, to support and guide the rotating shaft. They are commonly used in high-speed and high-precision applications, such as in machine tools and computer hard drives. 9. Plain bearings: Also known as bushings, these bearings consist of a smooth, cylindrical surface that rotates against a shaft. They are commonly used in low-speed and low-load applications, such as in hinges and pivots. 10. Ceramic bearings: These bearings use ceramic balls or rollers instead of steel ones, making them lighter, stronger, and more resistant to corrosion. They are commonly used in high-speed and high-temperature applications, such as in racing cars and aerospace equipment.
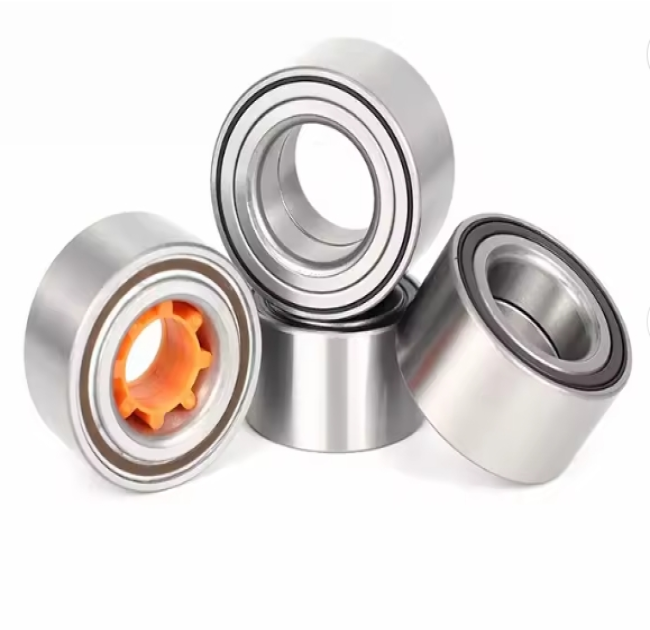
5.What is the benefit of using ceramic bearings?
1. Increased Speed and Efficiency: Ceramic bearings are smoother and have less friction than traditional steel bearings, allowing for faster and more efficient rotation. This can be especially beneficial in high-speed applications such as cycling or skateboarding. 2. Higher Durability: Ceramic bearings are made from a harder material than steel bearings, making them more resistant to wear and tear. This means they have a longer lifespan and require less frequent replacement. 3. Corrosion Resistance: Ceramic bearings are highly resistant to corrosion, making them ideal for use in harsh environments or in applications where they may be exposed to water or chemicals. 4. Lighter Weight: Ceramic bearings are typically lighter than steel bearings, which can be beneficial in applications where weight is a concern, such as in the aerospace industry. 5. Reduced Friction and Heat: The smooth surface of ceramic bearings reduces friction and heat buildup, which can help to prevent damage to the bearing and surrounding components. 6. Lower Maintenance: Due to their durability and resistance to wear, ceramic bearings require less maintenance and replacement compared to steel bearings, saving time and money in the long run. 7. Improved Performance: The reduced friction and heat of ceramic bearings can lead to improved overall performance in machines and equipment, resulting in better efficiency and productivity.
6.How do you calculate the expected lifespan of a bearing?
The expected lifespan of a bearing can be calculated using the following formula: L = (C/P)^3 x 10^6 Where: L = Expected lifespan (in hours) C = Basic dynamic load rating of the bearing (in Newtons) P = Applied load on the bearing (in Newtons) The basic dynamic load rating of a bearing can be obtained from the manufacturer's catalog or datasheet. The applied load on the bearing can be calculated by considering the weight of the rotating equipment, the speed of rotation, and any additional external forces acting on the bearing. It is important to note that this formula provides an estimate of the expected lifespan and may vary depending on the operating conditions and maintenance practices.
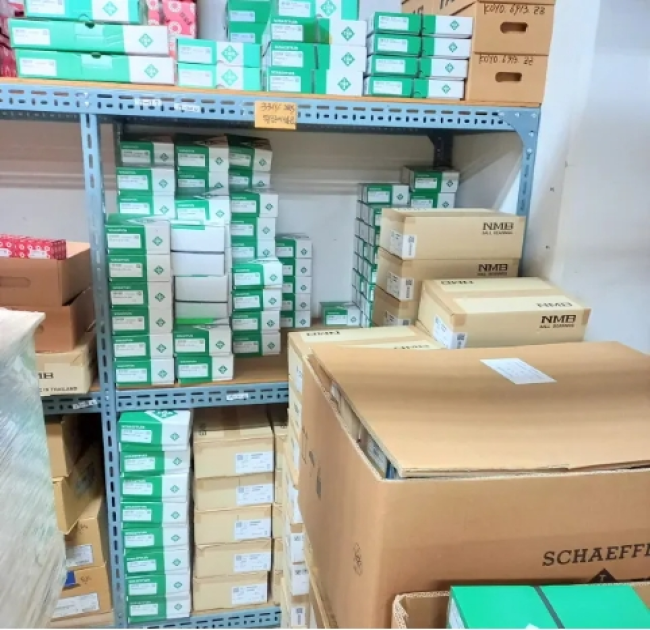
7.What is the difference between bearing life and bearing reliability?
Bearing life refers to the expected duration of time that a bearing can operate before it fails due to wear or damage. It is typically measured in hours or cycles of operation. Bearing reliability, on the other hand, refers to the probability that a bearing will operate without failure for a given period of time. It takes into account factors such as the quality of the bearing, the operating conditions, and maintenance practices. Reliability is often expressed as a percentage, with higher percentages indicating a lower likelihood of failure. In summary, bearing life is a measure of how long a bearing is expected to last, while bearing reliability is a measure of how likely it is to operate without failure for a given period of time.
8.How can you extend the lifespan of a bearing?
1. Proper lubrication: Regularly lubricating the bearing with the correct type and amount of lubricant can significantly extend its lifespan. This helps reduce friction and wear on the bearing. 2. Keep the bearing clean: Dirt, dust, and other contaminants can cause premature wear and damage to the bearing. Regularly cleaning the bearing and its surrounding area can help prevent this. 3. Proper installation: Make sure the bearing is installed correctly and according to the manufacturer's instructions. Improper installation can cause misalignment and excessive load on the bearing, leading to premature failure. 4. Avoid overloading: Bearings have a maximum load capacity, and exceeding this limit can cause damage and shorten their lifespan. Make sure to use the correct bearing for the application and avoid overloading it. 5. Regular maintenance: Regularly inspecting the bearing for signs of wear and tear can help identify any issues early on and prevent them from causing further damage. Replace worn or damaged bearings promptly. 6. Protect from moisture and corrosion: Moisture and corrosion can cause significant damage to bearings. Make sure to protect them from these elements by using appropriate seals and keeping them in a dry environment. 7. Proper handling and storage: When not in use, bearings should be stored in a clean, dry, and vibration-free environment. They should also be handled with care to avoid any damage. 8. Use compatible parts: When replacing bearings, make sure to use compatible parts from the same manufacturer. Mixing different brands or types of bearings can cause compatibility issues and lead to premature failure. 9. Monitor operating conditions: Keep an eye on the operating conditions of the bearing, such as temperature and speed. Excessive heat or high speeds can cause damage to the bearing, so it's essential to monitor and adjust as needed. 10. Train employees: Properly trained employees can help identify and address any issues with bearings before they become major problems. Make sure your employees are trained in proper bearing maintenance and handling techniques.
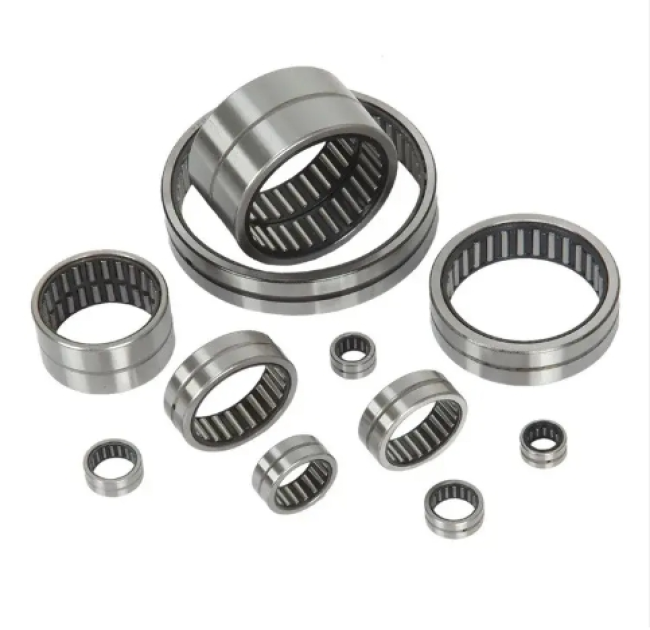
9.How does improper bearing installation impact its performance?
Improper bearing installation can have a significant impact on its performance in several ways: 1. Reduced load capacity: If the bearing is not installed correctly, it may not be able to handle the intended load, leading to premature failure and reduced performance. 2. Increased friction and heat generation: Incorrect installation can result in misalignment or uneven distribution of load, causing increased friction and heat generation. This can lead to accelerated wear and tear of the bearing and reduced performance. 3. Vibration and noise: Improper installation can cause the bearing to operate at an angle, resulting in vibration and noise. This can affect the overall performance of the machinery and lead to premature failure. 4. Reduced lifespan: A bearing that is not installed correctly may not be able to withstand the expected operating conditions, leading to premature failure and reduced lifespan. 5. Safety hazards: In some cases, improper bearing installation can result in catastrophic failure, posing a safety hazard to the operators and surrounding equipment. 6. Costly repairs and downtime: If a bearing fails due to improper installation, it can result in costly repairs and downtime, affecting the overall productivity and profitability of the machinery. Overall, improper bearing installation can significantly impact its performance, leading to reduced efficiency, increased maintenance costs, and safety risks. It is essential to follow proper installation procedures and guidelines to ensure optimal performance and longevity of the bearing.